Range Rover Classic Shell & Panel Restoration
Kingsley have a specialist in-house welding and metal workshop.
We can restore both the inner steel shell of Range Rovers and make TIG repairs on the outer alloy panels — all to the highest possible standard. This page is designed provide you with an insight into the typical exhaustive processes that we employ when undertaking classic Range Rover bodyshell restoration and hopefully provide an insight into the comprehensive work that goes into producing a Kingsley Re-engineered Range Rover body. We also do undertake repairs on client cars, but only on the understanding that we do the job properly to result in work produced to the highest standards.
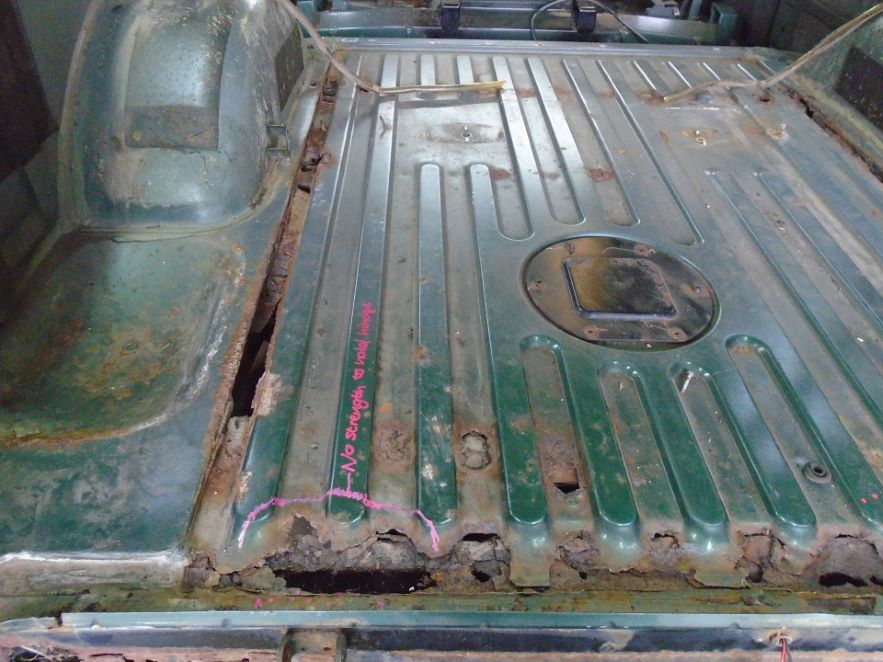
Identifying Corrosion
The team start by identifying all of the areas of corrosion on your car (which is normally very easy by checking to see if the carpet is wet if it has been raining recently!). We then remove and store the carpets, the under carpet sound deadening, the seats, the battery and the outer alloy panels as required.
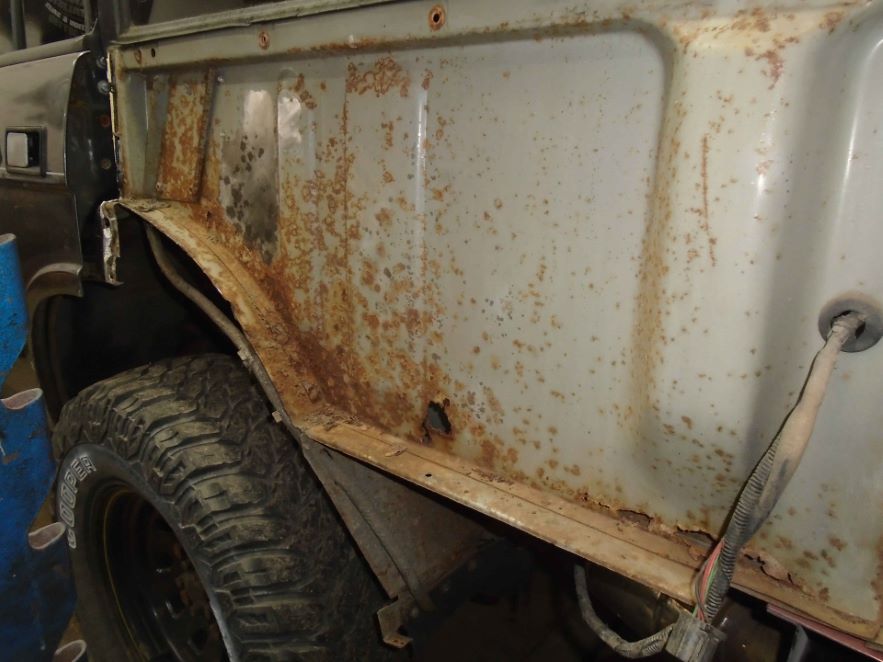
Dismantling the Vehicle
Once all of the corrosion has been identified and marked in yellow the vehicle is dismantled to allow access to the corroded areas.
Usually the minimum would be to remove the bumpers, bonnet, decker (or scuttle) panel, outer front wings, doors, rear wings, roof panel and lower tailgate then all of the interior trim remaining including the seats and carpets but depending upon the depth of the restoration and the amount of the corrosion we often dismantle to a completely bare bodyshell.
Each of the removed parts is further dismantled for the internal and component parts to be refurbished ie. the doors will have the mirror, waist seat, rubbing strip, door frame, door glass, window regulator, door handle, door lock, latch mechanism and door hinge removed and refurbished.
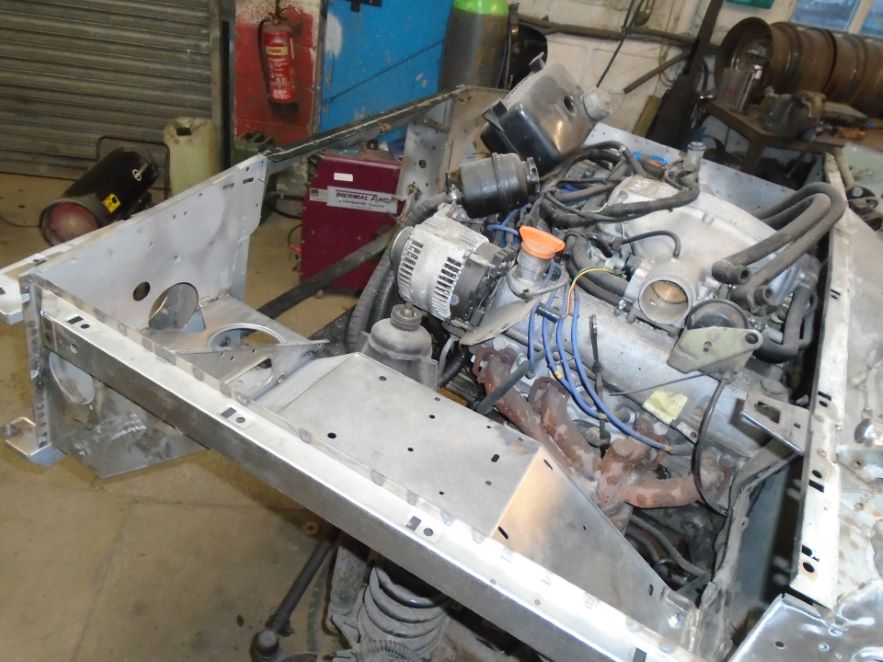
Repairing the Bodyshell
Our welding fabrication team construct custom replacement repair sections to the bodyshell in the relevant correct gauge steel, which they seamlessly butt weld into place.
Once welded we fully dress each weld so that it is flat and cannot be seen from either side. Once welded and the shell is structurally strong enough to be separated from the chassis we place it onto a wheeled dolly.
The repaired bodyshell then goes to the paint department to be bare metalled and prepared for blasting whilst the chassis, engine and running gear goes, depending upon the commissioned works, either into storage or back to the dismantling team to be further taken down for grit blasting and refurbishment.
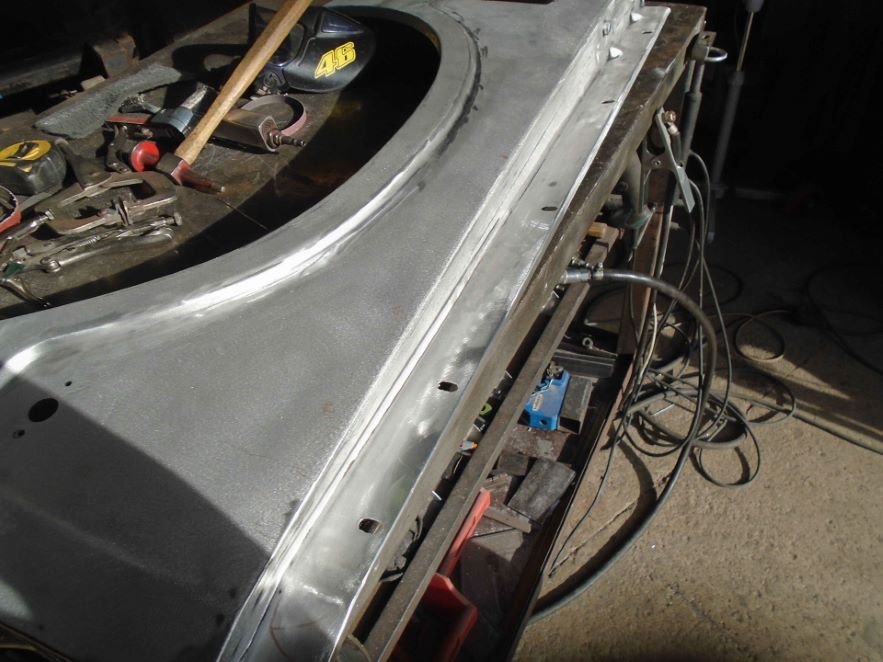
Liquid Penetrate Inspection (LPI)
Whilst the inner shell is being welded our in-house body shop ‘bare metal’ all of the removed body panels both on the inside and the outside for the body shop foreman to inspect for corrosion. Any panels which look ’suspect’ are then liquid penetrate inspection (LPI) tested.
LPI is based upon capillary action, where low surface tension fluid penetrates into clean and dry surface-breaking discontinuities. After adequate penetration time has been allowed, the excess penetrant is removed and a developer is applied. The developer helps to draw penetrant out of the flaw so that an invisible indication becomes visible to the inspector indicating the need for repair. This attention to detail guarantees that the paint will remain in excellent order with no ‘bubbling’ for years to come.
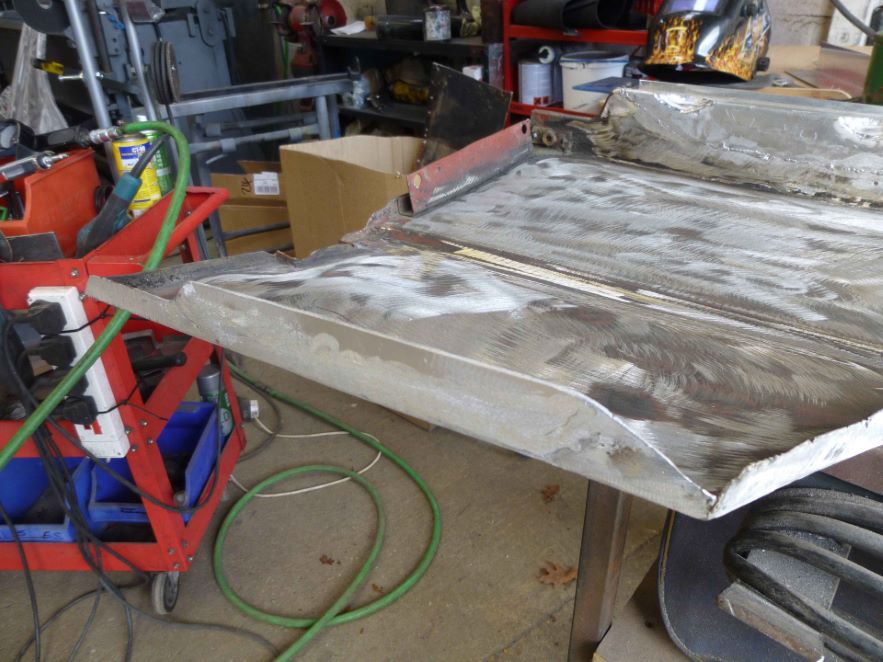
Exterior Panel Repairs
Exterior panels which have been identified with corrosion from the LPI testing are sent back to the welding and fabrication shop where the corrosion is removed by cutting out to good metal and new metal is seamlessly TIG or MIG butt welded into place and the welds dressed to make an invisible repair.
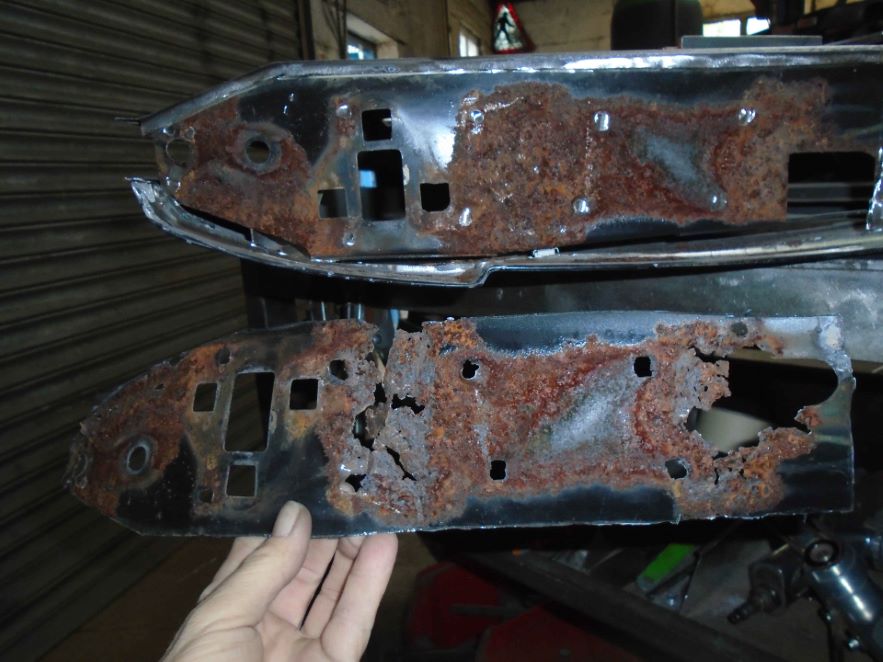
Range Rover Classic Door Reskinning
There is a challenge with Range Rover doors where the steel door body reacts with the‘Birmabright’ alloy outer skin which is manifested with‘bubbles’ in the paint or white aluminium corrosion breaking through the paint.
Up until now the only way to solve this is to replace the alloy door skins (which are unavailable) as the Birmabright door skin distorts when welded.
Thanks to the latest technology we are able to solve the issue of electrolytic corrosion on Range Rover doors by partially reskinning the section of the door skins which are corroding. We can re-skin your door as supply only from £670+VAT per door or prepared in primer ready to paint from £875+VAT per door or as part of your restoration. The metal workshop at Kingsley is also able to quote to restore your corroded doorcases.
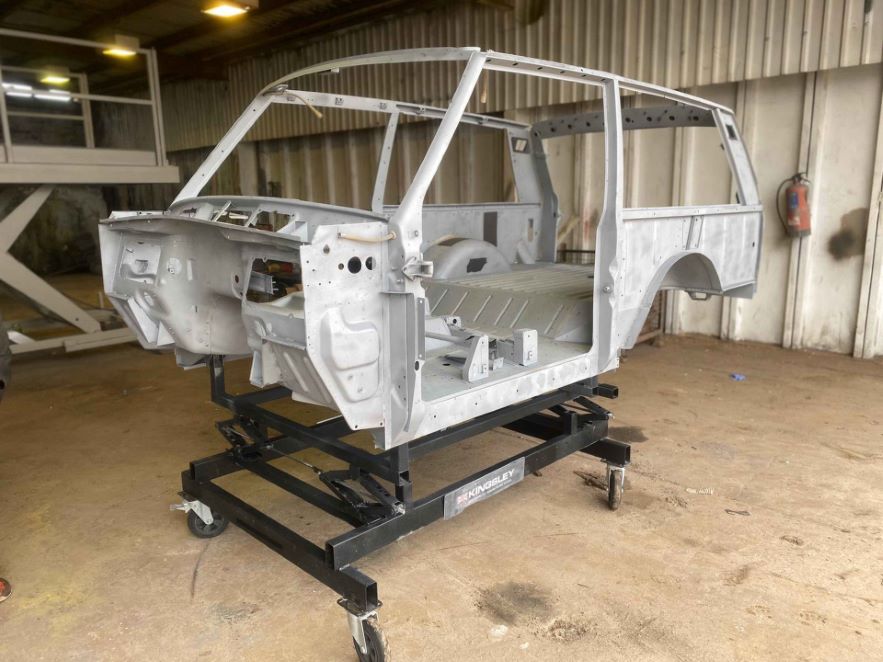
Bodyshell Blasting
Once the bodyshell is welded, we grit blast the bodyshell using Olivine, a naturally occurring silica free expendable material.
Grit blasting is a mild abrasive treatment which removes all surface contaminants, surface rust, edge burrs and coatings from the bodywork. We use the process as part of our Quality Control procedure to make sure there are no areas of corrosion or thinner metal on the shell have been missed — ensuring the future-proofing process of the main structure of your Range Rover Classic.
Once complete we prime the shell in Zinc Phosphate. Phosphating is used on steel parts for added corrosion resistance and to provide the perfect base Kingsley’s paintwork topcoats.
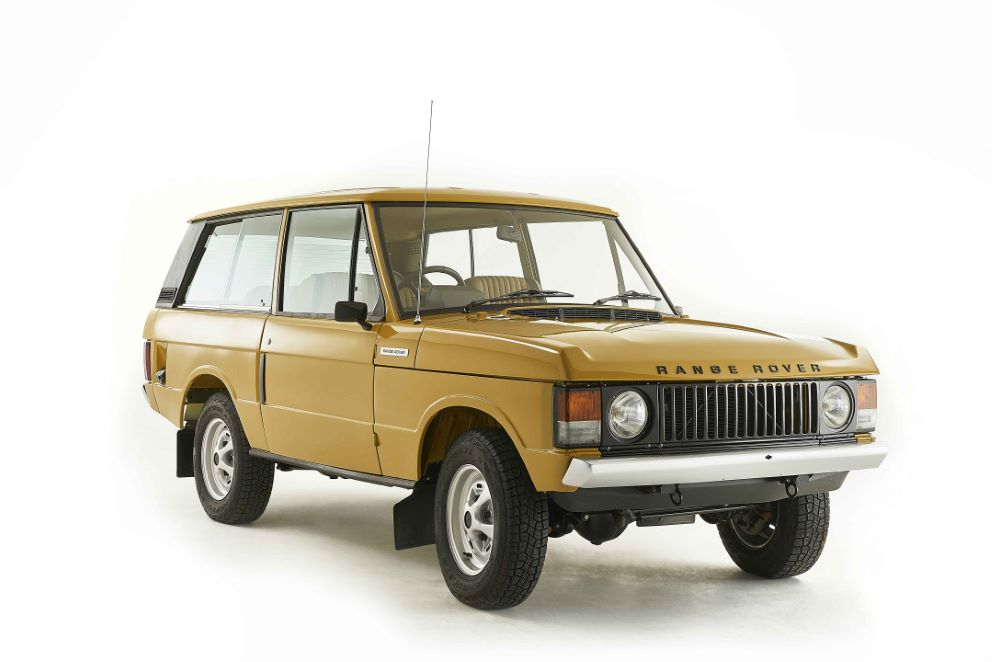
The Proof is in the Pudding
We are constantly restoring around 15 Range Rovers and have twenty reborn each year, if you are able to visit we can show you the before, during and after — the end results are quite simply outstanding!
Subscribe to our newsletter and learn about our latest news and updates.